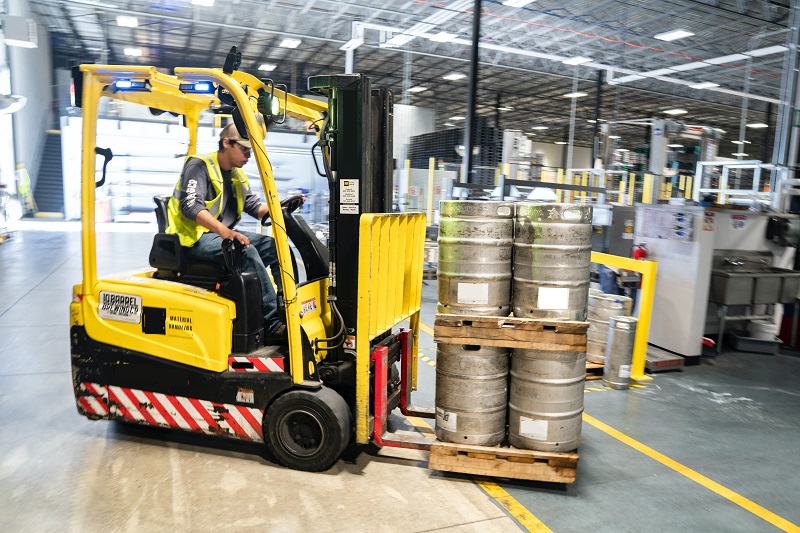
Being utterly dependable and critically important in large warehousing operations, electric forklifts often need regular care and repair to continue performing optimally. But have you ever contemplated what’s involved in these periodic check-ups and fixes? Are they simply a matter of replacing parts and tightening bolts, or is there much more complexity lurking beneath the surface?
The truth is, repairs involve a careful blend of technical knowledge, pragmatism, and most critically, attention to safety procedures. The centerpiece of our discussion today revolves around the crucial part – safety measures during electric forklift repairs. We will deep dive into the need for safety, what processes to implement, and how to ensure these guidelines are followed rigorously by your team.
Why Should Safety Be Emphasized In Forklift Repair Processes?Â
In the bustling environment of a warehouse or storage facility, forklift repairs can often become an overlooked area of safety concerns. The reason? Simply put, the tasks are often routine-oriented, occurring frequently enough to lull a sense of complacency. However, this is where potential dangers often lurk.
Firstly, electric forklifts repairs on high-capacity batteries, meaning any mishandling can lead to serious injuries or even fatal accidents. Secondly, the machine’s sheer bulk and weight make it a major hazard if not appropriately anchored or stabilized during repairs. Finally, over time, wear and tear can lead to unseen vulnerabilities that even seasoned technicians might overlook.
What Safety Measures Can Be Adopted?
Safety procedures during repair operations should be ingrained into the workflow of every single technician. Inculcation of safety-first mentalities, coupled with consistent refresher training, ensures everyone remains sharp and aware of existing and potential hazards.
Moreover, authenticity of parts is vital – cheap, knock-off replacements may come with tempting price tags, but put your forklifts and technicians at incredible risk. Engaging a certified forklift repair specialist or company, capable of providing authentic spare parts and skilled service personnel, is an ideal measure.
Incorporating Safety Protocol Standards
Adopting standardized procedures such as those outlined in ISO 9001 can help an organization structure a safety protocol that’s comprehensive, systematic, and effective. It should incorporate thorough risk assessments, regular safety audits, and continuous training programs.
Training the Forklift Repair Team
A well-trained team is the backbone of any safety-first culture. On-the-job sessions alongside theoretical courses provide employees with a solid understanding of their responsibilities and associated risks.
The Pitfalls Of Ignoring Safety Measures
When ignored, the ramifications can range from minor injuries to fatal accidents and expensive lawsuits. Not only that, but damage to forklifts could lead to costly downtimes and replacement costs, significantly impacting a company’s bottom line.
ConclusionÂ
In the end, ensuring utmost attention to safety measures during electric forklift repairs isn’t just about following regulations or ticking off a corporate checklist. It’s about genuinely caring for your workforce and building a culture where safety isn’t just a buzzword, but an intrinsic part of your organization’s DNA.
At the heart of it all, remember, the key to operating effectively is to ensure everyone leaves the workplace in the same condition, if not better, than when they arrived. And that alone is an investment worth making. Never underestimate the power of a safety-centric approach; the rewards go far beyond the immediate financial savings to foster a healthy, positive, and committed workplace. It’s safety first, always.